Bridge House, Croydon, Is Prefab Really Prefabulous?
Prefabricated homes have been available for years and date back at least a century. The Sears Roebuck index made and offered prefab homes to the public as early as 1908, and Prefab was later explored by famous twentieth-century architects, such as, Walter Gropius, Le Corbusier, Marcel Breuer, Frank Lloyd Wright, who saw the method as a likely solution to the dilemma of housing in modern society. Interest in Prefab grew in the first half of the twentieth-century, with the outburst of manufacturing expertise and the creation of the assembly line.
Historically the mention of prefabricated houses invokes memories of housing built to cover in the temporary a deficiency of housing in the UK following the World Wars.
The Government promised ‘homes fit for heroes’, however, negative public attitudes surfaced towards prefabricated housing because of substandard building materials used and poor workmanship.
A staggering 1 million of these homes were built during the 20th century and more than half a century on, many are still standing despite no foundations. A few are listed while others have been demolished.
Today people remember the shabby mobile classrooms as in, bitter cold in winter and like an oven in summer. Therefore, memories have rendered the concept of prefabricated houses an unattractive idea. Talk about the term prefabricated housing to an architect, and their eyes will beam with visions of fascinating contemporary homes. However, talk to the ordinary person on the street and people immediately think that we are going down the same path, a pretty hard image to shake off. The very factors that are presented as positive advantages of prefabricated homes became liabilities in the eyes of homeowners who wanted a durable appreciating asset.
An example can be found by looking at the prefabricated houses on Catford estate built by German and Italian prisoners of war in 1946.
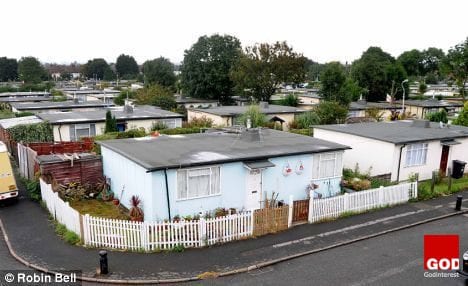
‘They were not built to last and need regular maintenance. They are just large sheds really and taking up a lot of space. They should really be demolished.’ (Drake 2008)
Over the ten years, Lewisham Council has tried to develop the site many times and a review found none of the dwellings met Decent Homes Standard.
So why do more and more developers choose prefabricated construction?
First and foremost – Speed. “It may take a bit longer in terms of design, preparation and planning but site based activities are taking up to 30% less time and allowing homes to reach the market sooner. Other reasons cited include, in order of preference:
- Design Quality
- Cost
- Previous Experience
- Funding
Source: Design and Modern Methods of Construction. The Housing Corporation and CABE 2004″
Bridge House (Example)
Croydon Vision 2020 is a regeneration programme by the London Borough of Croydon for the centre of Croydon in South London. The Old Town Masterplan focused on the area between the High Street and Roman Way, one of the oldest areas of Croydon.
Formerly the site of a telephone exchange, Bridge House is a £20 million development that has provided 27 private and 48 affordable apartments, above ground and mezzanine retail spaces.
The block wraps around an existing multi-storey car park and offers the opportunity for cafs and shops to open onto the new square. A mix of green and brown roofs, to support biodiversity, form part of a series of environmental measures and the scheme is to be of modular construction.
The Croydon chose the modular approach principally because of the speed of construction offered. The project began on site in the spring of 2006 and the 75 flats were stated to have been erected in approximately 26 days, vastly outperforming the time taken by traditional construction.
Client: Howard Holdings plc
Architect: AWW
Structures: Walsh Associates
Principal Supplier: MC First
Old Montague Street Student Accommodation
London needs over 30,000 new homes every year for the next 15 years to keep up with the demand from the people who wish to live and work in the city. Despite good housing output, figures published by the GLA show that there is a huge deficit in the number of affordable homes being produced, particularly larger homes.
A shortage of bricks is often cited as the main reason why developers are looking at new methods of construction to answer the demand for new homes. But brick is a major part of the London urban environment; planners often insist on this most familiar of materials, homeowners love its solid dependability. Therefore masonry is also becoming a modern technology to overcome the lack of skilled craftsmen available. Several companies have developed brickslip cladding systems which look like solid brickwork but need much less skill to install. Glued brickwork is another innovative approach introduced from Europe whose thin mortar joints produce a new sharper continental aesthetic.
Old Montague Street Student Accommodation
This Hall of Residence containing 219 Study bedrooms is set in the vibrant east end of London, just a few minutes walk from the Whitechapel Road the famous Brick Lane. The scheme consists of cluster flats of 6/7 bedrooms each sharing a kitchen, arranged over three floors above basement and ground floor commercial and ancillary accommodation. Provision of a formal courtyard for all access together with the vertical grouping of amenity space is an inherent part of the design. The accommodation is composed of offsite prefabricated pods which were brought to site finished with all fittings and fixtures clad with thin brick slip cladding.
Clients: Shaftesbury Housing Group and The London Institute
Architect: T P Bennett
Principal Supplier: Hanson Plc
Location: Don Gratton House, 82 Old Montague St, London E1 5NN
9 Suggestions for Overcoming Barriers to Good Design When Using Modern Methods of Construction (Mmc)
The term ‘Modern Methods of Construction’ (MMC) embraces a range of technologies involving various forms of prefabrication and off-site assembly.
MMC is increasingly regarded as a realistic means of improving quality, reducing time spent on-site, improving on-site safety and addressing skills shortages in the construction of UK housing.
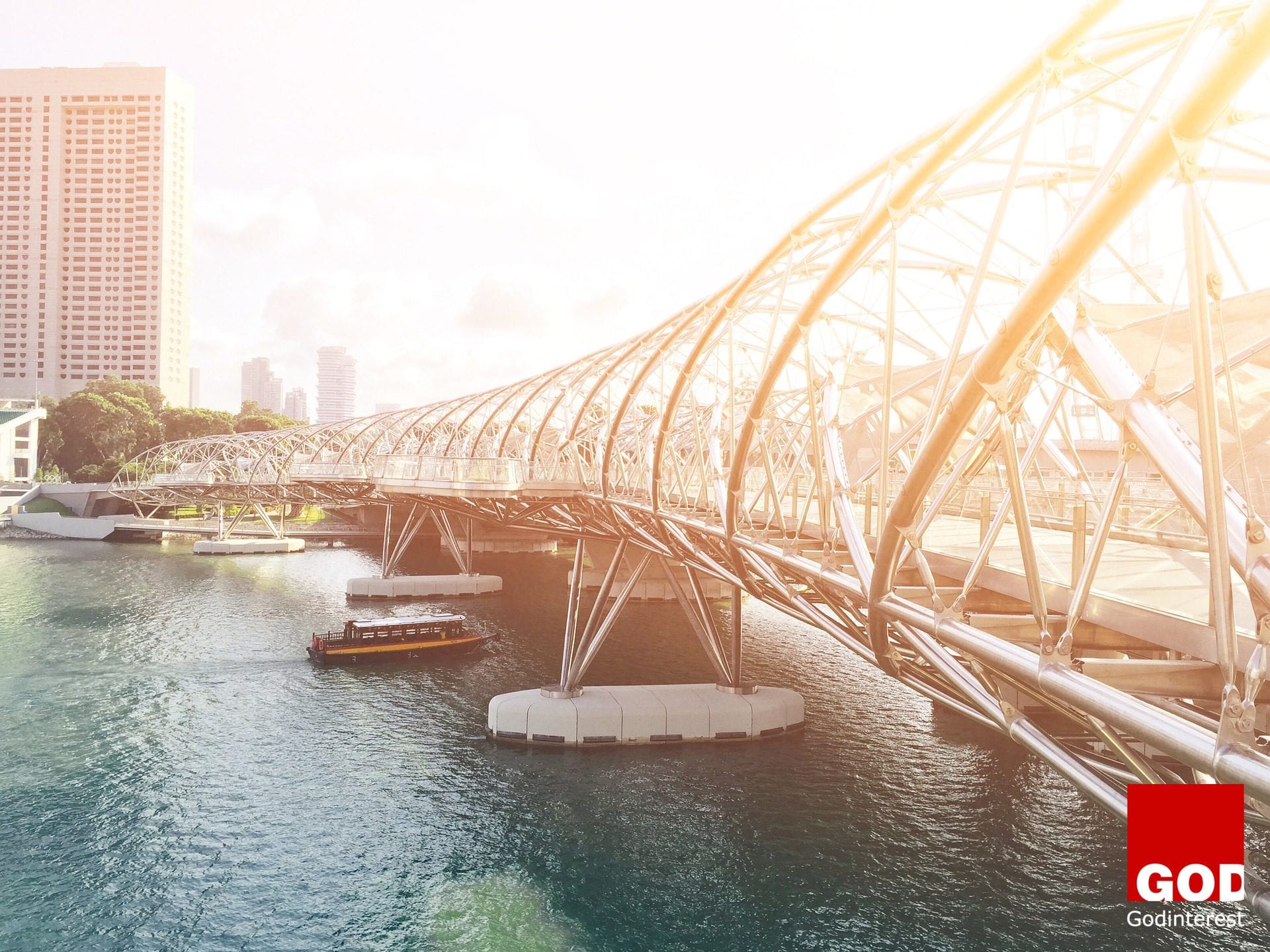
The variety of systems now available potentially allows the designer enough choice to sidestep problems deriving from constraints posed by the use of any one method. MMC systems, from closed-panel timber framed systems to bathroom pods are a palette from which designers can make choices. They are not necessarily stand-alone solutions that anticipate all the needs of an individual site and can be mixed and matched as appropriate.
These limitations are not obstacles to achieving the good design in MMC-based schemes, but may hinder the incorporation of more complex and innovative types of MMC from which greater overall benefits may be obtained which are considered under the following headings:
1. COST UNCERTAINTY
There is no doubt that, given products of comparable performance the key issue in purchases of MMC construction systems is the price. At present not enough is known about the potential costs of using volumetric and closed panel systems to enable confident specification at an early date. This inhibits designers from exploring the full potential of MMC systems. This is particularly true of the less repetitive, small, one-off scheme, where a smaller margin of benefits is gained from using MMC. The principal barrier to the uptake of MMC, therefore, seems to be the perception of cost uncertainty with respect to using more complex systems. Without doing substantial project-specific research, consultants and their clients simply do not know with enough degree of certainty how much the volumetric or closed panel systems are likely to cost, and what would be the savings to overall project costs produced by potential speed gains to offset against increased capital expenditure.
This is due to the complexity of assessing the ratio of cost of repetitive elements where pricing is relatively straightforward to the cost of adjusting elements or building in another method for the abnormal condition. Decisions to use innovative systems are likely to be made once designs are well progressed to enable teams to be more certain of costs. This can increase the potential for change or result in design compromise as the designer attempts to incorporate the specific limitations of a particular system in their design.
In an attempt to improve this situation, the MMC consultant and or clients could pull together a directory of MMC expanded to include cost comparison data. The huge range of variables involved inevitably makes this difficult, but a database of current construction cost information would be an invaluable resource.

2. PLANNING PROCESS AND EARLY COMMITMENT TO A SYSTEM
The time it can take to obtain planning permission has obvious implications both for project cost but also, in some circumstances, for architectural design innovation.
Most of the more complex types of MMC have an impact on dimensioning, the choice of external finish and detailing may have some effect on the buildings mass. Therefore, the construction system should be chosen prior to a planning application to avoid abortive work, redesign or amendment, or even resubmission for planning permission.
However, developers whose money is at risk, frequently hold off deciding on the construction technique until the last practicable moment, in order to get any advantage from fluctuations in material or component pricing.
Given the potential for lengthy duration of planning applications, this means that there is little incentive to prepare initial designs for planning with a prior decision to incorporate MMC firmly embedded. In cases where the developer has a financial or business link with the supplier, this is less likely to be the case. As the majority of commercial or residential developments involve some kind of arrangement with a developer, agreement on construction systems is often left to the stage after planning.
3. TIME INVESTMENT
Another very significant factor is the time investment required at the early stages of projects. This is needed to develop the design when the project is still at risk. There is a direct relationship between the scale and complexity of MMC component and the amount of time required to develop a design at an early stage.
The introduction of advanced or complex MMC techniques into the design process is potentially costly to the design team. A significant amount of research is needed to explore alternative systems, to obtain verification of suppliers’ credentials, investigate mortgage and insurance issues, visit previous sites, talk to system suppliers, obtain technical performance guidelines, understand junctions and interfaces, coordinate other consultants, obtain building control input and so on.
For a consultant, the only way of investing in this research is either through timely payment of increased fees by a visionary understanding client or through the anticipation of increased future productivity through repetition when a project is phased, or large enough, or likely to be followed by another similar project.
The potential of learning a system and then being able to repeat lessons learned efficiently is a powerful incentive for both client and consultant. By contrast, HTA’ s project at Basingstoke is an example of a phased project with a three to four-year duration allowed the design team to repeat various elements of the design, and the manufacturer to develop improved solutions to technical and supply problems.

4. INSUFFICIENT COMMUNICATION
Improved dialogue at the outset of the project is vital if design quality is to be maximised. Constraints and opportunities implicit within a particular system are more easily incorporated into design if partners communicate pre-planning. Increased early communication can be fostered through improved long-term partnering relationships.
Clients should also partner with a range of suppliers and architects so that choice and flexibility is not restricted.
5. INEXPERIENCE
Generally, the inexperienced client or design team will have to do more research, with the result that there is likely to be significant design development without a specific system being incorporated.
This is a disincentive to using a more complex system involving a higher proportion of MMC, where early decision making and knowledge of a system’ s capabilities have a decisive influence on the nature of the architecture. However, encouraging the take up of MMC through the use of a dedicated funding mechanism may assist clients in finding time for research into suitable MMC techniques.
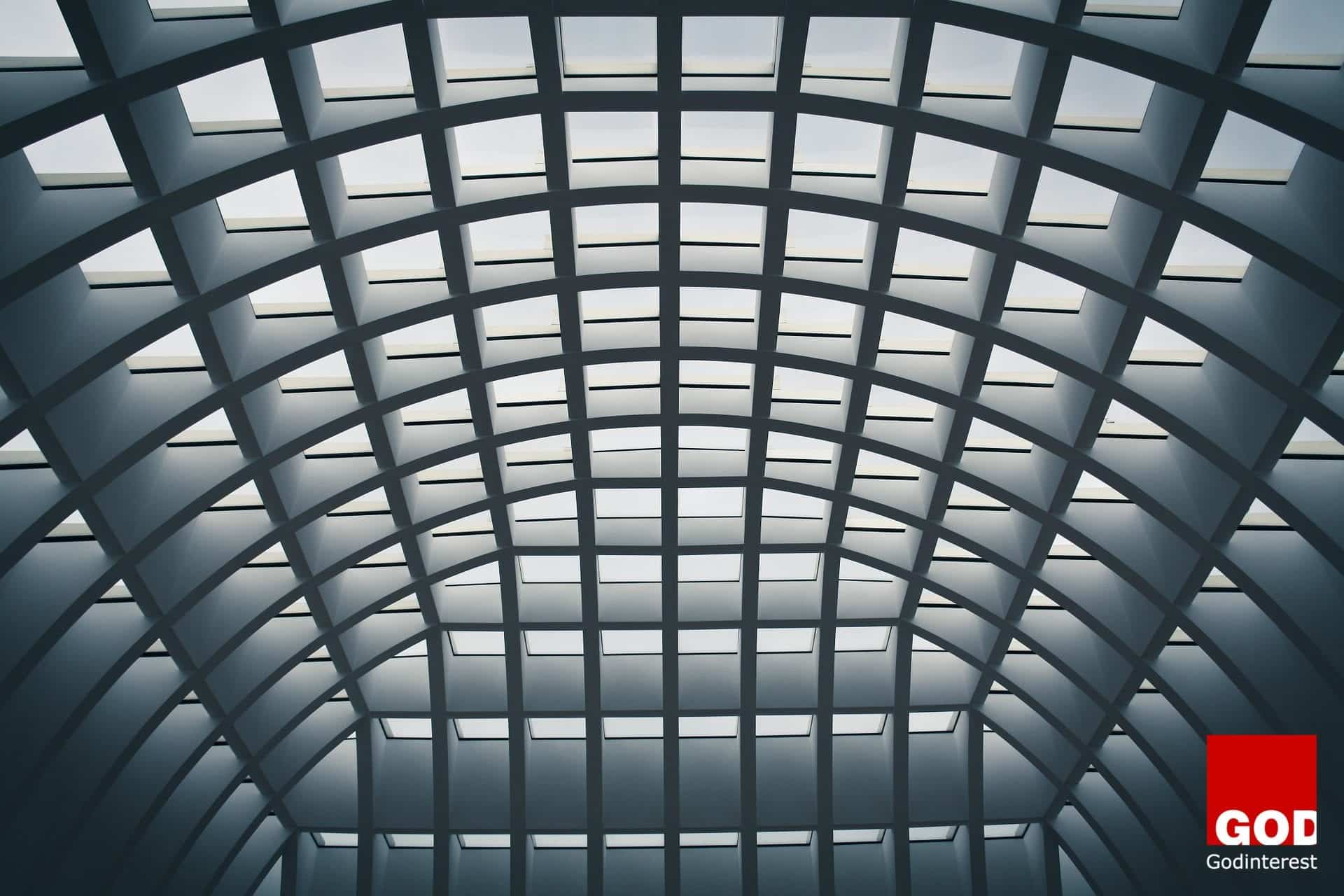
6. SUPPLIER’S ROLE
Site capacity studies and early stage pre-planning design studies could be undertaken directly by system suppliers on behalf of clients, cutting out the usual procedure of commissioning design work by independent consultants.
7. ASSUMPTIONS
There are a number of assumptions that are generally held about certain types of MMC that may have been valid at one time but are no longer true today. There is a need for reliable and up to date information comparing system criteria, performance data, timescales, lead in times, capacity, construction time, sequencing issues, limitations, and benefits.
Therefore it would be helpful if a forum for discussion and experience exchange was set up.
8. DEMONSTRATING THE BENEFITS OF MMC
There is still a large amount of skepticism about the need to go very far down the line with MMC. This is reflected in the acceptance of the desirability of maintaining or indeed enhancing the pool of traditional craft skills throughout the UK.
A balanced view is that there is a demonstrable need for the wider use of MMC which is recognized by both industry and government. The best way for clients and the public generally to become more confident and knowledgeable about the quality of design achievable through MMC is to see it demonstrated.
9. FINANCIAL INCENTIVES
There is no doubt that spreading the burden of investment through the life of a project helps to ensure a higher standard of specification and hence quality. In the Netherlands, a ‘ Green Financing’ system has been developed by the Dutch government that provides favorable loan finance when certain sustainable standards are reached. In the UK, the Gallions HA has pioneered a study of this, based on a scheme in Thamesmead, ‘ the Ecopark project’.
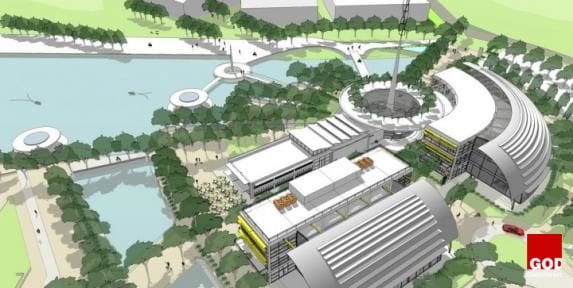
Prefab Comeback
Prefab housing suffers from bad stigma due to the fact that some people saw the prefabs as ugly and characterless, and were afraid they would become slums – hardly the promised housing fit for heroes following the second World War. However, building homes from pre-made parts can save time and money. The term prefab or prefabrication often evokes thoughts of poor construction, substandard living conditions and a long-standing “temporary” solution.
Prefab dwellings are making a comeback driven by a lack of affordable housing, a rapidly growing economy and changing demographic trends.
Methods Methods of Construction (Mmc) Offer Significant Potential to Minimise Construction Costs
The term ‘Modern Methods of Construction‘ refers to a collection of relatively new building construction techniques that aim to offer more advantages over traditional construction methods. Off-site construction (OSC) is a modern method of construction, based on off-site manufacturing of building elements.
With exponentially lower construction costs, quicker construction, reduced labor costs and having the ability to achieve zero defects, MMC is gaining a lot of attention as the potential answer to the UK’s housing crisis.
In a valiant attempt to strip away prefabricated housings’ bad rep are MMC with contemporary sleek designs, and constructed to withstand the test of time. MMC housing has the capability to deliver both quality and quantity housing to the tune of ‘ £50,000 per unit.
MMC units hold the promise of being extremely energy efficient and environmentally sustainable. Many versions of MMC take into account how to utilise natural resources and reduce each unit’s carbon footprint. In addition, MMC also addresses environmental concerns by creating much less waste than a standard brick-and-mortar project. While it is plausible that a traditional build could hire a waste removal company who would have the ability to recycle up to 90 percent of the construction waste; with MMC projects, this will automatically happen.

There have already been a number of successful examples of MMC housing constructed in various parts of the United Kingdom. The M-house (pronounced “mouse”) is designed and constructed to last an upwards of 100 years. While Architect Alford Hall have created quality MMC apartment buildings proudly showcasing a patio and private entrance for each flat.
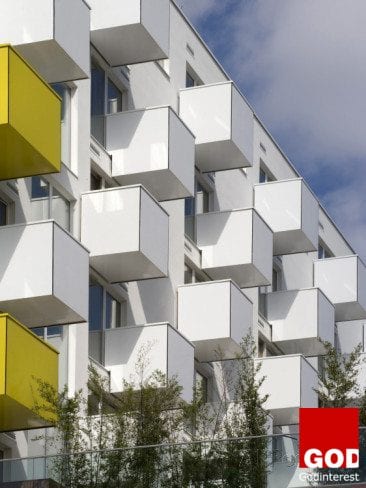

While many of the MMC homes are still in their early years the upkeep and maintenance will be reduced by 50% since the OSC process lowers the risk of non-conformities.
MMC homes are being fabricated and designed to accommodate many different lifestyles, such as, two-story homes, tall six-story apartment buildings, single-family homes and log cabins are all available options for families looking at MMC.
While there is a plethora of design options available all MMC OSC projects have a common theme. The internal workings of the homes are fabricated off-site, while only the “outer skin” comes to fruition on-site. To even further streamline the process, it has been suggested that having a “catalog of pre-selected materials increases supplier relationships and makes the design process more streamlined.”
With the small sample available with progressive MMC systems, it is currently reasonable to conclude that using modern methods of construction to build homes can cost more than traditional home building procedures; due to the need for specialised MMC design consultants. However, outside of costs, MMC remains a faster home building method than traditional brick and block house building and is slowly becoming a relevant front-runner to answer the UK’s housing shortage.