The term ‘Modern Methods of Construction’ (MMC) embraces a range of technologies involving various forms of prefabrication and off-site assembly.
MMC is increasingly regarded as a realistic means of improving quality, reducing time spent on-site, improving on-site safety and addressing skills shortages in the construction of UK housing.
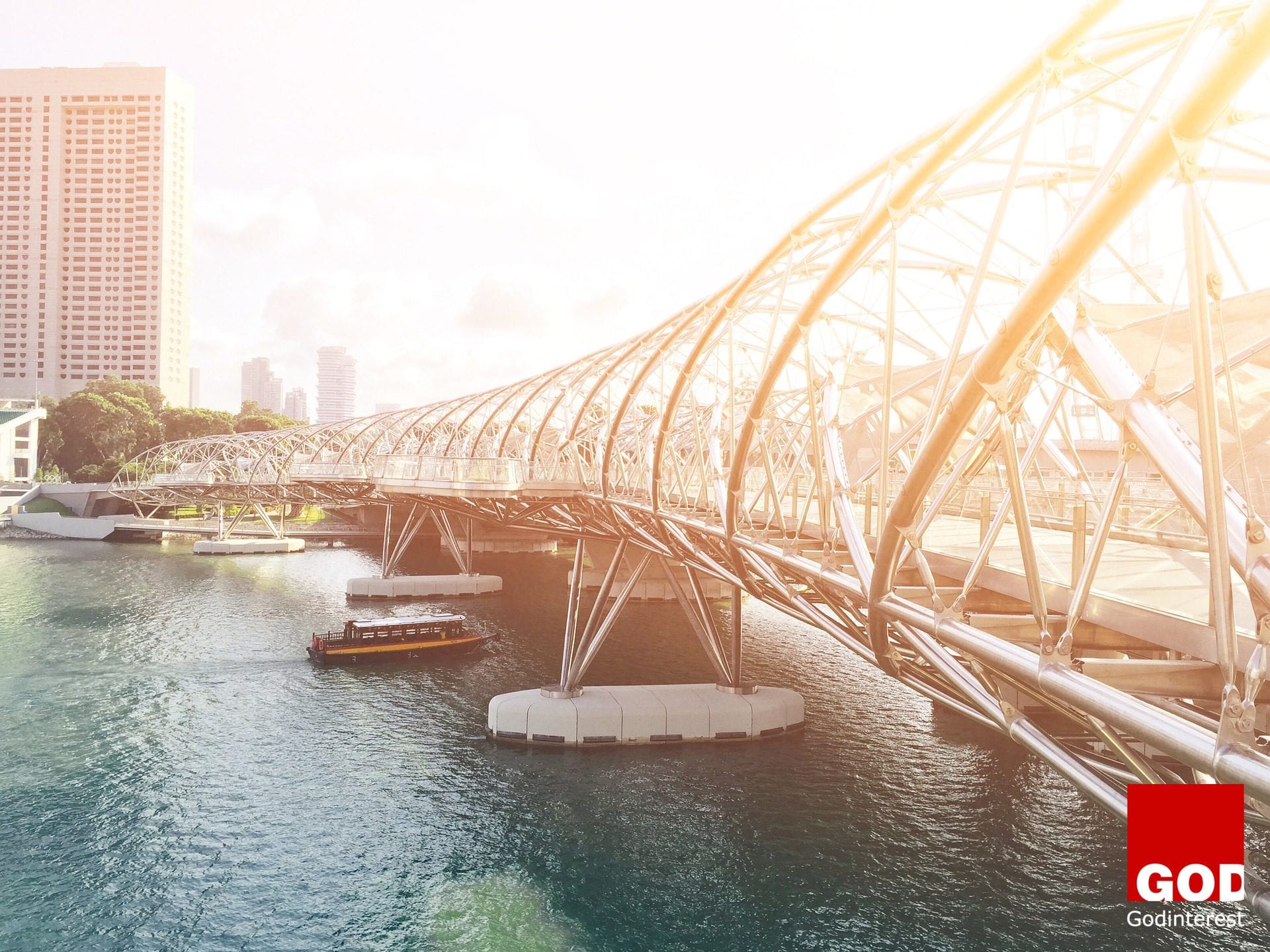
The variety of systems now available potentially allows the designer enough choice to sidestep problems deriving from constraints posed by the use of any one method. MMC systems, from closed-panel timber framed systems to bathroom pods are a palette from which designers can make choices. They are not necessarily stand-alone solutions that anticipate all the needs of an individual site and can be mixed and matched as appropriate.
These limitations are not obstacles to achieving the good design in MMC-based schemes, but may hinder the incorporation of more complex and innovative types of MMC from which greater overall benefits may be obtained which are considered under the following headings:
1. COST UNCERTAINTY
There is no doubt that, given products of comparable performance the key issue in purchases of MMC construction systems is the price. At present not enough is known about the potential costs of using volumetric and closed panel systems to enable confident specification at an early date. This inhibits designers from exploring the full potential of MMC systems. This is particularly true of the less repetitive, small, one-off scheme, where a smaller margin of benefits is gained from using MMC. The principal barrier to the uptake of MMC, therefore, seems to be the perception of cost uncertainty with respect to using more complex systems. Without doing substantial project-specific research, consultants and their clients simply do not know with enough degree of certainty how much the volumetric or closed panel systems are likely to cost, and what would be the savings to overall project costs produced by potential speed gains to offset against increased capital expenditure.
This is due to the complexity of assessing the ratio of cost of repetitive elements where pricing is relatively straightforward to the cost of adjusting elements or building in another method for the abnormal condition. Decisions to use innovative systems are likely to be made once designs are well progressed to enable teams to be more certain of costs. This can increase the potential for change or result in design compromise as the designer attempts to incorporate the specific limitations of a particular system in their design.
In an attempt to improve this situation, the MMC consultant and or clients could pull together a directory of MMC expanded to include cost comparison data. The huge range of variables involved inevitably makes this difficult, but a database of current construction cost information would be an invaluable resource.

2. PLANNING PROCESS AND EARLY COMMITMENT TO A SYSTEM
The time it can take to obtain planning permission has obvious implications both for project cost but also, in some circumstances, for architectural design innovation.
Most of the more complex types of MMC have an impact on dimensioning, the choice of external finish and detailing may have some effect on the buildings mass. Therefore, the construction system should be chosen prior to a planning application to avoid abortive work, redesign or amendment, or even resubmission for planning permission.
However, developers whose money is at risk, frequently hold off deciding on the construction technique until the last practicable moment, in order to get any advantage from fluctuations in material or component pricing.
Given the potential for lengthy duration of planning applications, this means that there is little incentive to prepare initial designs for planning with a prior decision to incorporate MMC firmly embedded. In cases where the developer has a financial or business link with the supplier, this is less likely to be the case. As the majority of commercial or residential developments involve some kind of arrangement with a developer, agreement on construction systems is often left to the stage after planning.
3. TIME INVESTMENT
Another very significant factor is the time investment required at the early stages of projects. This is needed to develop the design when the project is still at risk. There is a direct relationship between the scale and complexity of MMC component and the amount of time required to develop a design at an early stage.
The introduction of advanced or complex MMC techniques into the design process is potentially costly to the design team. A significant amount of research is needed to explore alternative systems, to obtain verification of suppliers’ credentials, investigate mortgage and insurance issues, visit previous sites, talk to system suppliers, obtain technical performance guidelines, understand junctions and interfaces, coordinate other consultants, obtain building control input and so on.
For a consultant, the only way of investing in this research is either through timely payment of increased fees by a visionary understanding client or through the anticipation of increased future productivity through repetition when a project is phased, or large enough, or likely to be followed by another similar project.
The potential of learning a system and then being able to repeat lessons learned efficiently is a powerful incentive for both client and consultant. By contrast, HTA’ s project at Basingstoke is an example of a phased project with a three to four-year duration allowed the design team to repeat various elements of the design, and the manufacturer to develop improved solutions to technical and supply problems.

4. INSUFFICIENT COMMUNICATION
Improved dialogue at the outset of the project is vital if design quality is to be maximised. Constraints and opportunities implicit within a particular system are more easily incorporated into design if partners communicate pre-planning. Increased early communication can be fostered through improved long-term partnering relationships.
Clients should also partner with a range of suppliers and architects so that choice and flexibility is not restricted.
5. INEXPERIENCE
Generally, the inexperienced client or design team will have to do more research, with the result that there is likely to be significant design development without a specific system being incorporated.
This is a disincentive to using a more complex system involving a higher proportion of MMC, where early decision making and knowledge of a system’ s capabilities have a decisive influence on the nature of the architecture. However, encouraging the take up of MMC through the use of a dedicated funding mechanism may assist clients in finding time for research into suitable MMC techniques.
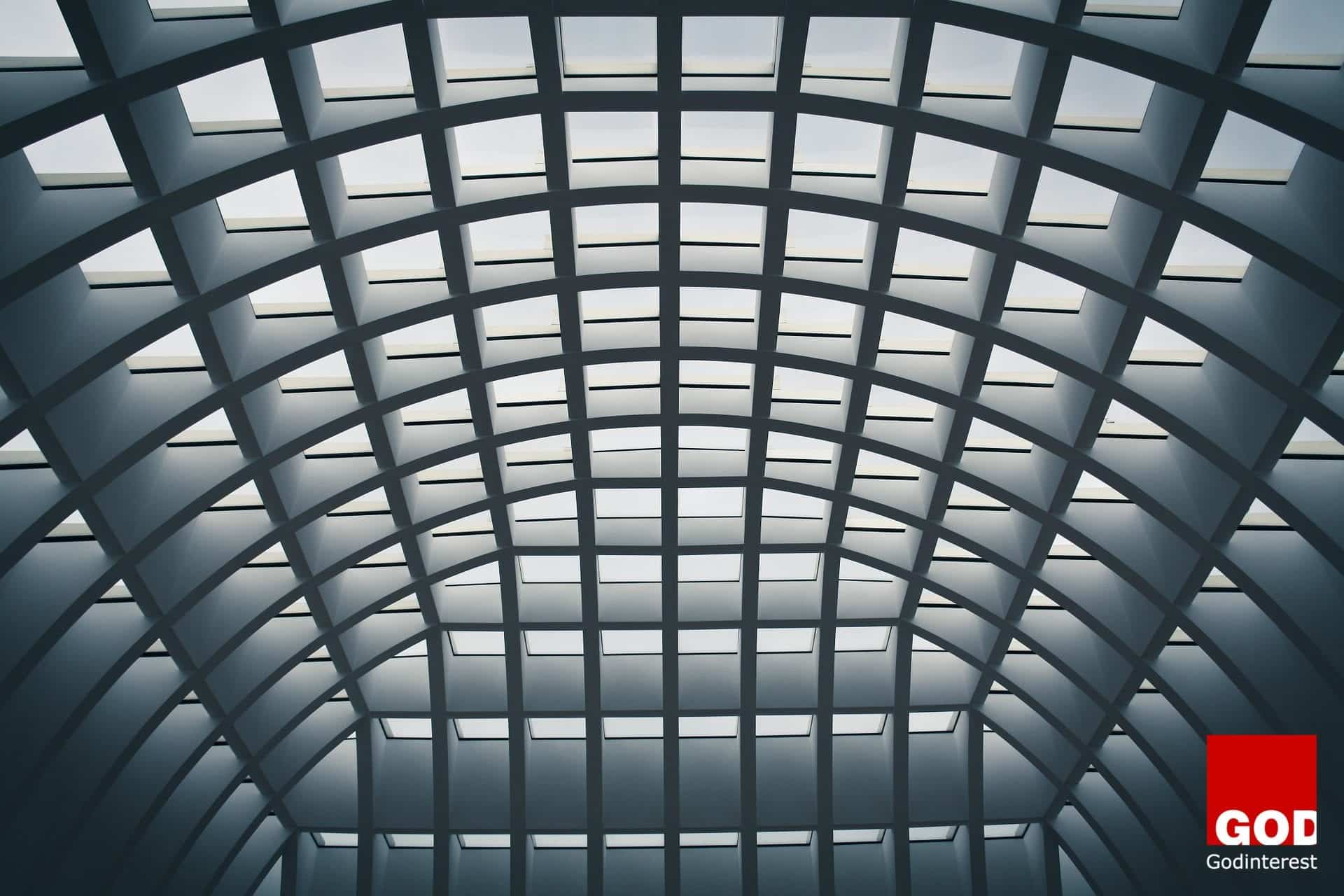
6. SUPPLIER’S ROLE
Site capacity studies and early stage pre-planning design studies could be undertaken directly by system suppliers on behalf of clients, cutting out the usual procedure of commissioning design work by independent consultants.
7. ASSUMPTIONS
There are a number of assumptions that are generally held about certain types of MMC that may have been valid at one time but are no longer true today. There is a need for reliable and up to date information comparing system criteria, performance data, timescales, lead in times, capacity, construction time, sequencing issues, limitations, and benefits.
Therefore it would be helpful if a forum for discussion and experience exchange was set up.
8. DEMONSTRATING THE BENEFITS OF MMC
There is still a large amount of skepticism about the need to go very far down the line with MMC. This is reflected in the acceptance of the desirability of maintaining or indeed enhancing the pool of traditional craft skills throughout the UK.
A balanced view is that there is a demonstrable need for the wider use of MMC which is recognized by both industry and government. The best way for clients and the public generally to become more confident and knowledgeable about the quality of design achievable through MMC is to see it demonstrated.
9. FINANCIAL INCENTIVES
There is no doubt that spreading the burden of investment through the life of a project helps to ensure a higher standard of specification and hence quality. In the Netherlands, a ‘ Green Financing’ system has been developed by the Dutch government that provides favorable loan finance when certain sustainable standards are reached. In the UK, the Gallions HA has pioneered a study of this, based on a scheme in Thamesmead, ‘ the Ecopark project’.
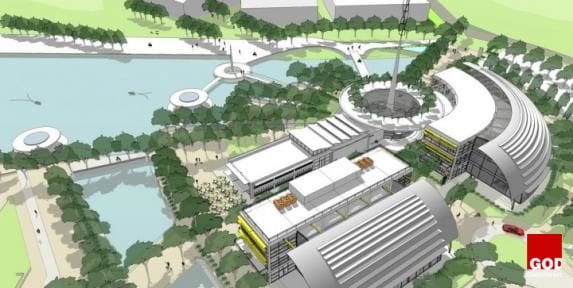